-
-
-
Total payment:
-
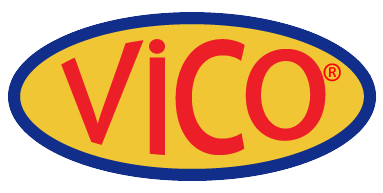
Casting Defects
Posted by Vico Casting Export Company Limited at 15/12/2023
Casting flaws are abnormalities or errors that occur during the casting process and result in unwanted characteristics in the final cast product. These flaws can be created by a variety of circumstances and manifest themselves in a variety of ways. Here are some examples of frequent casting flaws, as well as their causes and potential solutions:
Porosity: Causes: The presence of gas pockets within the cast material causes porosity. It can happen because to moisture, poor gating or venting, insufficient mold permeability, or severe turbulence during pouring.
Solutions include proper mold drying, effective gating and venting systems, enhancing mold permeability, limiting pouring speed and turbulence, and selecting appropriate alloys with low gas content.
Causes of Shrinkage: Shrinkage flaws arise when there is an insufficient supply of material during the solidification process, resulting in voids or shrinkage cavities in the cast item. It can be caused by insufficient riser size, poor gating, or quick cooling.
Solutions include proper gating and riser design, guaranteeing enough material supply, managing solidification rates with insulating materials or chilling, and optimizing cooling rates.
Cold shuts are generated by the partial fusing of two metal streams during the pouring process. It happens when the metal cools and hardens before fully fusing, leaving a visible line or seam in the cast portion.
Solutions include using proper gating and pouring processes, maintaining optimum metal temperature and fluidity, and modifying mold design to encourage total fusion.
Misruns happen when the molten metal does not entirely fill the mold cavity, resulting in an incomplete casting. This could be due to a low pouring temperature, insufficient gating, or poor venting.
Solutions include raising the pouring temperature, upgrading the gating and venting systems, employing proper pouring processes, and assuring proper mold rigidity.
Inclusions:
Causes: Foreign materials or impurities embedded in the casting, such as sand, slag, or oxides, are examples of inclusions. They can be produced by insufficient mold cavity cleaning, poor gating, or the presence of contaminants in the molten metal.
Solutions include thorough mold cleaning, efficient gating and pouring processes, precise metal handling and filtration, and the use of high-quality materials.
These are only a few instances of typical casting flaws. It's vital to remember that any fault can have multiple causes, and the solutions will differ based on the exact circumstances and materials employed. Quality control procedures, regular inspections, and process optimization can all help to reduce casting faults and enhance overall cast product quality.