-
-
-
Total payment:
-
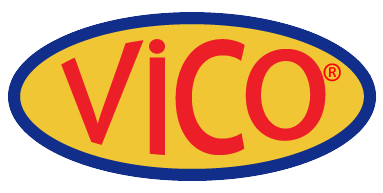
Cast Steel Production: Properties and Composition
Posted by Vico Casting Export Company Limited at 16/02/2022
Testing and inspection at the foundry
Cast steel is a ferrous alloy with a maximum carbon content of approximately 0.75%. Steel castings are solid metal objects produced by filling the void within a mold with liquid steel. They are available in many of the same carbon and alloy steels that can be produced as wrought metals. Mechanical properties for cast steel are generally lower than wrought steel, but with the same chemical composition. Cast steel compensates for this disadvantage with its ability to form complex shapes in fewer steps.
Properties of cast steel
Cast steels can be produced with a wide range of properties. The physical properties of cast steel change significantly depending on chemical composition and heat treatment. They are selected to match the performance requirements of the intended application.
- Hardness: The ability of a material to withstand abrasion. Carbon content determines the maximum hardness obtainable in steel, or hardenability.
- Strength: The amount of force necessary to deform a material. Higher carbon content and hardness result in steel with higher strength.
- Ductility: The ability of a metal to deform under tensile stress. Lower carbon content and less hardness result in steel with higher ductility.
- Toughness: The ability to withstand stress. Increased ductility is usually associated with better toughness. Toughness can be adjusted with the addition of alloying metals and heat treatment.
- Wear resistance: The resistance of a material to friction and use. Cast steel exhibits similar wear resistance to that of wrought steels of similar composition. The addition of alloying elements such as molybdenum and chromium can increase wear resistance.
- Corrosion resistance: The resistance of a material against oxidization and rust. Cast steel exhibits similar corrosion resistance to that of wrought steel. High-alloy steels with elevated levels of chromium and nickel are highly oxidation resistant.
- Machinability: The ease at which a steel casting can change shape by removing material through machining (cutting, grinding, or drilling). Machinability is influenced by hardness, strength, thermal conductivity, and thermal expansion.
- Weldability: The ability of a steel casting to be welded without defects. Weldability is primarily dependent on the steel casting’s chemical composition and heat treatment.
- High-temperature properties: Steels operating at temperatures above ambient are subject to degraded mechanical properties and early failure due to oxidation, hydrogen damage, sulfite scaling, and carbide instability.
- Low-temperature properties: The toughness of cast steel is severely reduced at low temperatures. Alloying and specialized heat treatments can improve a casting’s ability to withstand loads and stresses.
Chemical composition of cast steel
The chemical composition of cast steel has a significant bearing on performance properties and is often used to classify steel or assign standard designations. Cast steels can be broken into two broad categories—carbon cast steel and alloyed cast steel.
Carbon cast steel
Like wrought steels, carbon cast steels can be classified according to their carbon content. Low-carbon cast steel (0.2% carbon) is relatively soft and not readily heat-treatable. Medium carbon cast steel (0.2–0.5% carbon) is somewhat harder and amenable to strengthening by heat treatment. High carbon cast steel (0.5% carbon) is used when maximum hardness and wear resistance are desired.
Alloyed cast steel
Alloyed cast steel is categorized as either low- or high-alloy. Low-alloy cast steel (≤ 8% alloy content) behaves similarly to normal carbon steel, but with higher hardenability. High-alloy cast steel (> 8% alloy content) is designed to produce a specific property, such as corrosion resistance, heat resistance, or wear resistance.
Common high-alloy steels include stainless steel (> 10.5% chromium) and Hadfield’s manganese steel (11–15% manganese). The addition of chromium, which forms a passivation layer of chromium oxide when exposed to oxygen, gives stainless steel excellent corrosion resistance. The manganese content in Hadfield’s steel provides high strength and resistance to abrasion upon hard work.
Cast steel grades
Steel grades have been created by standards organizations such as ASTM International, the American Iron and Steel Institute, and the Society of Automotive Engineers to classify steels with specific chemical compositions and resulting physical properties. Foundries may develop their own internal grades of steel to meet user demand for specific properties or to standardize specific production grades.
The specifications for wrought steels have often been used to classify different cast alloys by their principal alloying elements. However, cast steels do not necessarily follow wrought steel compositions. The silicon and manganese contents are frequently higher in cast steels compared with their wrought equivalents. In addition to their predominantly higher levels of silicon and manganese, alloyed cast steels use aluminum, titanium, and zirconium for de-oxidation during the casting process. Aluminum is predominantly used as a de-oxidizer for its effectiveness and relatively low cost.
Cast steel production
The practice of casting steel dates back to the late 1750s, much later than the casting of other metals. The high melting point of steel, and the lack of technology available to melt and process metals, delayed the development of a steel casting industry. These challenges were overcome by advances in furnace technology.
Furnaces are refractory lined vessels that contain the “charge,” which is the material to be melted and provides energy for melting. There are two furnace types used in a modern steel foundry: electric arc and induction.
Electric arc furnace
The electric arc furnace melts batches of metal referred to as “heats” by means of an electric arc between graphite electrodes. The charge passes directly between the electrodes, exposing them to thermal energy from the ongoing electrical discharge.
Electric arc furnaces follow a tap-to-tap operating cycle:
- Furnace charging: Load of steel scrap and alloys are added to the furnace.
- Melting: Steel is melted by supplying energy to the furnace interior. Electrical energy is supplied through graphite electrodes and is usually the largest contributor to steel melting operations. Chemical energy is supplied through oxy-fuel burners and oxygen lances.
- Refining: Oxygen is injected to remove impurities and other dissolved gasses during the melting process.
- De-slagging: Excess slag, which often contains undesirable impurities, is removed from the bath prior to tap out. De-slagging can also take place within the ladle prior to pouring.
- Tapping (or tap out): Metal is removed from the furnace by tilting the furnace and pouring the metal into a transfer vessel such as a ladle.
- Furnace turn-around: Tap out and preparation is completed for the next furnace charge cycle.
Continuous additional steps are often taken at various stages in this process to further de-oxidize the steel and to remove slag from the metal prior to pouring. The steel’s chemistry may need to be adjusted to account for alloy depletion during an extended tap-out.
Induction furnace
An induction furnace is an electrical furnace where heat energy is transferred by induction. A copper coil surrounds the nonconductive charge container, and an alternating current is run through the coil to create an electromagnetic induction within the charge.
Induction furnaces are capable of melting most metals, and they can be operated with minimal melt loss. The disadvantage is that little refining of the metal is possible. Unlike an electric arc furnace, steel cannot be transformed.
Modern steel foundries frequently utilize recycled steel scrap to reduce the cost and environmental impact of casting production. Obsolete cars, mechanical components, and similar items are separated, sized, and shipped to foundries as scrap. This is combined with internal scrap generated in the casting process and combined with various alloying elements to charge the melting furnace.
Heat treatment
After the casting is solidified, removed from the mold, and cleaned, the physical properties of cast steel are developed by proper heat treatment.
- Annealing: Heating steel castings to a specific temperature, holding for a specific period of time, and then slowly cooling.
- Normalizing: Similar to annealing, steel castings are cooled in the open air, sometimes with fans. This helps the castings to achieve higher strengths.
- Quenching: Similar to normalizing, but cooling takes place at a much more rapid pace using forced air. Water or oils are used as the quench medium.
- Tempering (or stress relieving): Technique used to relieve internal stresses from within castings. These stresses can appear during the casting process, or during strengthening or hardening heat treatments such as normalizing or quenching. Stress relieving involves heating the castings to a temperature well below the annealing temperature, holding it at that temperature, and then slowing cooling.
Cast steel inspection
Steel castings are often subject to inspections to verify specific physical properties such as dimensional accuracy, cast surface finish condition, and internal soundness. In addition, the chemical composition must also be inspected. Chemical composition is dramatically affected by minor alloying elements added to the material. Cast steel alloys are susceptible to variations in their chemical composition, so chemical analyses are required to verify the exact chemical composition prior to casting. A small sample of molten metal is poured into a mold and analyzed.
Dimensional accuracy
Dimensional inspections are carried out to make sure that the castings produced to meet the customer’s dimensional requirements and tolerances including allowances for machining. It may sometimes be necessary to destroy sample castings to take measurements of interior dimensions.
Surface finish condition
Casting surface finish inspections are employed to explore the aesthetic appearance of castings. They look for flaws in the surface and sub-surface of the castings that may not be obvious visually. The surface finish of a steel casting may be influenced by the type of pattern, molding sand, and mold coating used, as well as the weight of the casting and methods of cleaning.
Internal soundness
All castings have some level of defects present, and the soundness specification determines the acceptable defect threshold. Over-specification of the maximum allowable defect level will lead to higher scrap rates and higher casting costs. Under-specification of the maximum allowable defect level can lead to failure.
Three common internal defects that occur in steel castings are:
- Porosity: Voids in the steel casting that are characterized by smooth, shiny interior walls. Porosity is generally a result of gas evolution or gas entrapment during the casting process.
- Inclusions: Pieces of foreign material in the casting. Inclusion can be metallic, intermetallic, or non-metallic. Inclusions can come from within the mold (debris, sand, or core materials), or can travel into the mold during the pouring of the casting.
- Shrinkage: Vacancy or area of low density typically internal to the casting. It is caused by a molten island of material that does not have enough feed metal to supply it during the solidification process. Shrinkage cavities are characterized by a rough crystalline interior surface.
Chemical analysis
Chemical analysis of cast steels is usually performed by wet chemical analysis methods or spectrochemical methods. Wet chemical analysis is most often used to determine the composition of small specimens, or to verify product analysis post-production. Contrastingly, analysis with a spectrometer is well-suited to the routine and rapid determination of the chemical composition of larger samples in a busy production foundry environment. Foundries can undertake chemical analysis at both the heat and product level.
Heat analysis
During heat analysis, a small sample of liquid cast steel is ladled from the furnace, allowed to solidify, and then analyzed for chemical composition using spectrochemical analysis. If the composition of alloying elements is not correct, quick adjustments can be made in the furnace or ladle prior to casting. Once correct, a heat analysis is generally considered to be an accurate representation of the composition of the entire heat of the metal. However, variations in chemical composition are expected due to the segregation of alloying elements, and the time it takes to pour off the heat of steel. Oxidation of certain elements may occur during the pouring process.
Product analysis
Product analysis is performed for specific chemical analysis verification, as the composition of individual castings poured may not entirely conform to the applicable specification. This can happen even if the product was poured from a heat of steel where the heat analysis was correct. Industry practices and standards do allow for some variation between heat analysis and product analysis.
Cast steel testing
A variety of mechanical properties can be achieved for carbon and alloy steel castings by altering the composition and heat treatments of cast steels. Foundries utilize specialized testing methods to check mechanical properties prior to product completion.
When it comes to casting steel testing, there are two types of testing used in the industry: destructive and non-destructive testing. Destructive testing requires the destruction of a test casting to visually determine the internal soundness of a part. This method only provides information on the condition of the piece tested, and does not ensure that other pieces will be sound. Non-destructive testing is employed to verify the internal and external soundness of casting without damaging the casting itself. Once the casting passes the tests, it can be used for its intended application.
Tensile properties
Tensile properties for steel castings are an indication of a casting’s ability to withstand loads under slow loading conditions. Tensile properties are measured using a representative cast sample that is subject to controlled tensile loading—pulling forces exerted on either end of the tensile bar—until failure. Upon failure, tensile properties are examined.
Bend properties
Bend properties identify a casting’s ductility by using a rectangular representative sample bent around a pin to a specific angle. The resulting bent bar is observed to check for objectionable cracking.
Impact properties
Impact properties are a measure of toughness resulting from testing the energy required to break a standard notched sample. The more energy required to break the sample, the tougher the cast material.
Hardness
Hardness is a measure of a casting’s resistance to penetration using indentation tests. It is a property that indicates the wear and abrasion resistance of cast steels. Hardness testing can also provide an easy, routine method to test for indications of tensile strength in a production environment. A hardness scale test result will normally correlate closely with tensile strength properties.