-
-
-
Total payment:
-
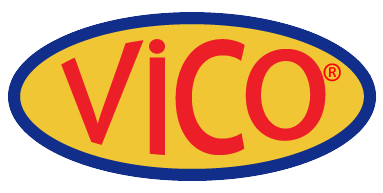
Foundry and Casting
Posted by Vico Casting Export Company Limited at 19/11/2022
A foundry is a metal casting manufacturing facility. Metals are cast into shapes by melting them into a liquid, pouring the metal into a mold, and then removing the mold material or casting once the metal has set and cooled. Aluminum and cast iron are the most commonly treated metals. Other metals, such as bronze, steel, magnesium, copper, tin, and zinc, are also used in foundries to make castings.
Casting is a manufacturing method that entails putting a liquid material into a mold with a hollow hole of the desired shape and letting it to harden. The solidified item, also known as a casting, is ejected or broken out of the mold to complete the process.
Melting
Melting is done in a furnace. The furnace is charged with virgin material, external scrap, internal scrap, and alloying elements. The term "virgin material" refers to commercially pure forms of the primary metal used to create a specific alloy. Alloying elements are either pure forms of an alloying element, such as electrolytic nickel, or limited-composition alloys, such as ferroalloys or master alloys.
Material from other forming processes, such as punching, forging, or machining, is considered external scrap. Internal scrap includes gates, risers, and damaged castings. Melting the charge, refining the melt, adjusting the melt chemistry, and tapping into a transport vessel are all part of the process.
To avoid casting defects, molten metal is refined to remove harmful gases and elements. During the melting process, material is added to bring the final chemistry within a specific range specified by industry and/or internal standards. Final chemical modifications are made during the tap.
Furnace
Several specialised furnaces are used to melt the metal. Furnaces are refractory lined vessels that contain the material to be melted and provide the energy to melt it. Modern furnace types include electric arc furnaces (EAF), induction furnaces, cupolas, reverberatory, and crucible furnaces. Furnace choice is dependent on the alloy system and quantities produced. For ferrous materials, EAFs, cupolas, and induction furnaces are commonly used. Reverberatory and crucible furnaces are common for producing aluminum castings.
Furnace design is a complex process that can be optimized based on a variety of factors. Foundry furnaces can range in size from a few ounces to hundreds of tons, and they are designed based on the metals to be melted. Furnaces must also be designed around the fuel used to achieve the desired temperature. Melting furnaces can reach 327° Celsius for low temperature melting point alloys like zinc or tin. For these temperatures, electricity, propane, or natural gas are typically used. The furnace must be designed for temperatures above 1600° Celsius for high melting point alloys such as steel or nickel-based alloys. Electricity or coke can be used to generate these high temperatures.
Degassing
A degassing step is frequently required in the case of aluminum alloys to lower the amount of hydrogen in the liquid metal. If the hydrogen content in the melt is too high, the resulting casting will have gas porosity, reducing its mechanical characteristics. Bubble argon or nitrogen into the melt to efficiently remove hydrogen. Foundries employ a variety of equipment to do this.
When the bubbles rise to the surface of the melt, they collect the dissolved hydrogen and transport it to the top. Various instruments are used to determine the amount of hydrogen present. In addition, the density of the aluminum sample is computed to determine the quantity of hydrogen dissolved in it.