-
-
-
Total payment:
-
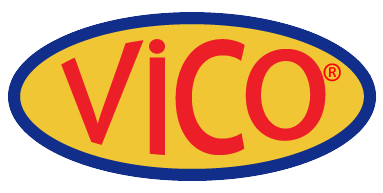
Burnt-on sand
Posted by Vico Casting Export Company Limited at 30/12/2022
This flaw can arise in any casting produced by a sand molding method, regardless of the material employed. This defect has also occurred in the core areas; nevertheless, it is difficult to distinguish it from the penetration phenomenon.
Materials cast at high temperatures, for example, are substantially more prone to this flaw than aluminum casting alloys. This fault is most common in thick-walled, heavy castings and/or at high-temperature locations, such as around the gate.
This flaw is distinguished by thin sand crusts on the casting surface (or in the core area) or by a constant, thin layer of sand covering the whole casting. These scorched sand areas can only be removed by grinding, not abrasive blasting.
This flaw develops when smelt may freely infiltrate the mold wall in the crevices between the grains of sand at the metal-mold interface during the casting process. As a result, the surface has a high degree of roughness in some areas or all throughout.
Burnt sand can be caused by uneven sand compaction (see compaction), too high metalo-static pressure (too high casting height), too high casting temperatures, too high degree of refractory lining (too high oolitization), or too low sintering point of the basic mold material. Furthermore, too coarse grain size and a lack of fine-grain substances, as well as a high degree of wetting of the mold surface by the casting metal, could be key sources of this type of fault.
Prevention
1. Defect detection is feasible by testing, such as for mold density, density distribution, permeability to gas, and examination of the sintering performance of mold material components.
2. Decreasing wetness of the mold surface due to an increase in glossy carbon-forming chemicals (carbon dust) while maintaining a reducing environment in the mold cavity.
3. Determine the degree of oolitization and, if necessary, add more sand.
4. Testing the quantitative bentonite addition for oolitization and reducing the amount if necessary.
5. Checking the proportion of dust in the conditioning system and lowering it as needed in relation to the binder quantity.
6. Using pure quartz sands (SiO2 concentration > 99.5%), because the degree of impurities has a significant impact on melt formation and consequently sintering results.
7. Ensuring even mold compaction; most importantly, preventing local variances in compaction.
8. Avoiding excessive casting temperatures and metalostatic stresses.
9. Applying a suitable face coat to the mold's vulnerable areas, or the entire mold if necessary.