-
-
-
Total payment:
-
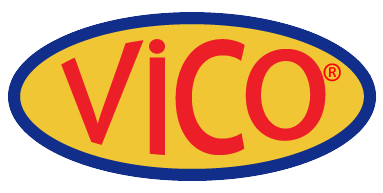
Lost foam casting
Posted by Vico Casting Export Company Limited at 16/12/2022
What is lost foam casting?
Lost foam casting is a method of producing intricate metal components and parts in which molten metal evaporates through a foam mold held steady with sand.
The technique begins with a polystyrene foam mold, which can be carved, machined from a foam block, or manufactured via an injection molding process.
Process to make lost foam pattern
First, a pattern is created out of polystyrene foam. This type of foam is essential in this casting procedure. It has a good thermal insulator and chemical resistance, allowing it to work normally at temperatures below 75 degrees Celsius.
The foam template is partially formed and put together for highly realistic casting patterns. Foundries frequently hand-cut or machine designs from a solid foam block for modest volumes. A hot wire foam cutter can be used if the pattern is simple enough.
Polystyrene beads are pumped under low pressure into a pre-heated aluminum mold. Following that, steam is introduced, causing the polystyrene to expand even more to fill the empty cavity and produce the pattern or portion. The final design contains 97.5% air and 2.5% polystyrene.
Casting process
After forming the pattern, it is coated with insulation paint, placed in a flask, surrounded by un-bonded sand, and compacted.
The covering paint strengthens the mold surface and protects it from erosion and breakage. The flask, on the other hand, is specially built for this approach so that when the molten metal is put into the mold, the gas produced by foam burning is totally evacuated.
The foam design is burned away after molten metal is poured into it, and the casting is created.
Advantages of lost foam casting
- It is capable of casting complex castings.
- It is useful for ensuring great precision and a clean surface finish.
- Casting using the lost foam process ensures that there are almost no faults or flaws.
- Because it requires fewer processes, this approach is generally less expensive than investment casting. Foundries can save a lot of money on labor and production by using the lost foam method.
Disadvantages of lost foam casting
- Firstly, the pattern costs can be significant for low volume applications.
- Another issue is that the patterns are readily broken or deformed because to their low strength.
Application
The lost foam technique can be used on a variety of materials, including alloy steel, carbon steel, alloy cast iron, ferrous alloy, and alloy aluminum.
Ignore a few drawbacks, there are many advantages found in the lost foam approach. This technology is frequently preferred to cast sophisticated and detailed items due to its precise casting ability.
It is used in a wide range of industries, including the arts, computer technology, agricultural, national security, automotive, and civil spheres.
The lost foam casting process is ideal for numerous cast items such as cylinder heads, cylinder blocks, pipe fittings, valves, fire hydrants, motor starters, 3D models, gearbox details, and more.
Lost foam casting is also used to produce highly intricate and complex lamp posts, gas burners, fences, pump housing, aluminum castings, pan supports, and other items.