-
-
-
Total payment:
-
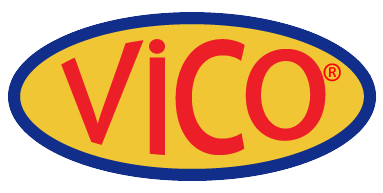
Causes and measures for slag inclusion defect in casting
Posted by Vico Casting Export Company Limited at 13/12/2022
Causes of slag inclusion:
- After treating the liquid iron with magnesium and rare earth, a series of reactions between the sulfur, oxygen, magnesium, and rare earth in the molten iron will occur, forming sulfide, oxide, magnesium silicate, and other non-metallic inclusions. These inclusions have a lower mass density than molten iron. The slagging is incomplete or the temperature of the molten iron is low after spheroidizing treatment. The inclusions either stay in the molten iron or eventually float up. Slag inclusion will form after pouring if it is too late to be eliminated.
- Because magnesium is easily oxidized, numerous oxygen atoms are adsorbed on the surface of molten iron after spheroidization, and iron atoms can be activated to oxidize the molten iron and form an oxide coating on its surface. Because the oxide coating is solid-liquid, it is difficult to remove when scraping slag. When the molten iron is left in the ladle after being poured, poured, and flows into the cavity, it oxidizes due to contact with the surrounding air and moisture in the molding sand. When the molten iron rolls, the oxide coating is split into bits, floats upward, and collects on the casting's surface. Furthermore, during the flotation process, sulfide particles dispersed in molten iron can be absorbed and gathered together on the casting's surface layer to form slag inclusion.
Measures to prevent slag inclusion:
- Reduce the residual magnesium and sulfur mass fractions in molten iron. Because magnesium and sulfur both raise the oxide film's conjunctival temperature. As a result, the larger the mass percentage of residual magnesium and sulfur in molten iron at the same pouring temperature, the more severe the slag inclusion.
- Make sure there is a sufficient mass percentage of residual rare earth. Because rare earth has the ability to lower the conjunctival temperature of the oxide coating. However, excessive residual rare earth presence will cause graphite form to deteriorate.
- Molten iron is added during the spheroidizing process. Secondary slag development can be decreased by adding 0.3% cryolite to the surface of molten iron.