-
-
-
Total payment:
-
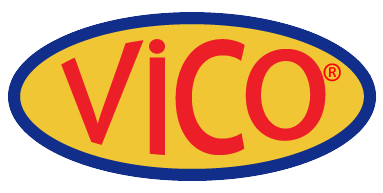
Cold crack and warpage in casting
Posted by Vico Casting Export Company Limited at 14/12/2022
Characteristics
- Cold crack: It is also a straight or curved crack on the casting's surface with little oxidation on the crack's surface. The majority of them can be found in the inner sharp corner transition, the thick and thin portions, and the joint between the inner gate and the casting. The naked eye, fluorescence inspection, and X-ray inspection can all detect it.
- Warpage: The overall shape and size of the casting or its individual components change, which can be measured with the naked eye or a measuring device.
Causes
Cold crack, warpage, and hot crack all form in distinct ways. The internal stress of the cooling shrinkage of the casting stopped by the mold or core at low temperature causes the cold fracture, which is greater than the strength of the alloy at this temperature. There will be no crack and only warping deformation if the internal stress value only surpasses the alloy liquid's yield limit at this moment.
Preventions
- Improve the casting's design structure, prevent abrupt changes in acute angle and thick section to thin section structure, and try to cool all portions of the casting uniformly and simultaneously.
- Take all possible precautions to ensure that castings cool uniformly and concurrently.
- Choose the appropriate shape and size of cold iron, as well as its optimum setting position, based on the shape of the thick components.
- To avoid local overheating, choose the correct position for injecting alloy liquid.
- Pouring temperature should be reduced properly.
- Use a riser and a chiller together to raise the temperature of the casting.
- Attempt to make the castings solidify in order.
- The riser is inserted into the thickest area of the casting, and insulation material is plastered on top to extend the solidification period.
- Place the cold iron or quench material on the casting's thickest section.
- Use a bottom casting pouring mechanism in conjunction with a high mold.
- Reduce the alloy liquid pouring temperature properly.
- Reduce sand mold strength while increasing yield
- Change from dry sand to wet sand mold
- Reduce the sand mold and core's compactness.
- Use collapsible molding sand instead of strong molding sand
- Reduce the size of the core frame and outline to prevent the casting from shrinking.
- Use a hollow core to increase yield.
- The cold or hot rectification process is used to restore the warped casting to its original shape, depending on the shape and degree of warping.
- If none of the preceding solutions work, an alloy with high temperature and high strength with a narrow crystallization interval (i.e. a restricted temperature range of quasi solid phase) can be used.