-
-
-
Total payment:
-
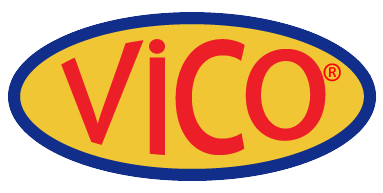
Metal penetration
Posted by Vico Casting Export Company Limited at 22/12/2022
As a result of physical/chemical interactions between melt and molding material components, this fault may arise with all molds manufactured using sand molding procedures (particularly green sand molding processes), regardless of material.
Melting phases are caused by reactions between metal and molding material, which result in scorched sand (sintering) and metal penetration (figures 1 and 2). This fault is most common in the casting of cast alloy steel. The human eye can easily see it on the casting. Copper-tin and zinc alloys are also vulnerable.
Metal penetrations occur most frequently around the borders of the sand mold or sand core, where the metal remains liquid for a longer period of time due to the geometry of the casting and the molds become extremely hot.
Metal penetration is a chemical penetration when compared to true mechanical/physical penetration. Burnt sand refers to the possible production of thin sand crusts comprised of individual quartz grains clinging to the casting (sintering). Metal penetration occurs when this thin and eventually extremely securely adherent layer is composed of molten sand, with the entire surface resembling pox.
It is difficult to tell the difference between conventional and metal penetration. Metal penetration is always followed by standard penetration and sintering.
On the one hand, the wetting tension during metal penetration can be modified in such a way that the penetration pressure (see Penetration) dips below the existing metallostatic pressure, significantly enhancing penetration on the casting. Melting phases, on the other hand, may occur as a result of reactions between metal and molding material, with ambient oxygen in the mold cavity and in the mold material pores playing a crucial role in this process. The production of silicate layers is caused by these melting phases (metal penetrations).
Measures of prevention
1. Test-based recording of the sinter behavior of bentonite, basic mold material, and mold material combinations is advised for defect avoidance. In any event, the sinter behavior of these components should be optimal.
2. Molding sand must be devoid of impurities that allow for slag reaction and the development of low-melting slag.
3. Increase the molding material's temperature resistance by adding new sand (to reduce oolitization); do not use or add sand containing impurities.
4. It is advantageous to use chemically neutral basic molding materials, such as chromite sand, instead of quartz sand.
5. Careful coating of molds and cores to avoid minor cracks in the coating layer; if necessary, increase coating thickness.
6. The development of reactive oxides and slag should be avoided by adding adequate components creating lustrous carbon
7. Any procedures employed to avoid conventional penetration have a beneficial influence on metal penetration prevention.