-
-
-
Total payment:
-
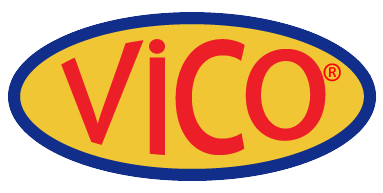
Characteristics of lost foam casting
Posted by Vico Casting Export Company Limited at 17/01/2023
High dimensional correctness
The casting is made all at once in the lost foam casting technique. Because it does not need to take the shape of a sand casting and does not require a parting surface or a sand core, the castings produced have no dimensional deviation, burr, flash, or draft angle. It is a shaping method with great dimensional shape precision and surface quality.
High production efficiency
The molding cycle is short because there is no need for sand mixing and sand mixing in the traditional sand mold casting process; when molding, there is no parting surface and sand core, which not only simplifies the process, but also reduces operations such as box splitting, box closing, core lowering, and mold turnover, but also enables the pouring of multiple parts in one box. As a result, this advantage is particularly pronounced for castings with a large manufacturing batch and complex geometry.
Easy for product design
Because the foam pattern may be used for following bonding process to build parts with difficult geometry that can be made at once by employing lost foam casting technique, lost foam casting can increase the overall performance of the product. Furthermore, lost foam casting eliminates the necessity for a separating surface and a sand core, improving the design freedom of goods with complex shapes.
Cleaner production
The filling of molten metal leads to the combustion of the foam pattern to decompose, the amount of gas generated by decomposition is small, the emission duration is short, it is easier to burn and purify, and the product after purification is environmentally safe. Because the lost foam casting mold employs negative pressure to compact dry sand, the labor intensity of cleaning falling sand is minimized, and the recovery rate of old sand is also very high, improving the foundry industry's working environment.
Improve casting quality and reduce scrap rate
Because lost foam casting does not require a separating surface or mold taking, flaws such as improper box, burr, and flash can be avoided. Furthermore, unlike traditional sand casting, lost foam casting employs dry sand and does not require the addition of a binder, moisture, or other additives, which decreases casting faults. Furthermore, vacuum negative pressure pouring is employed in lost foam casting, which improves the density of the casting structure because the negative pressure improves mold filling and liquid metal feeding capacity.
Wide applicability
Lost foam castings can be used for cast iron and steel castings, as well as aluminum and copper castings. Castings with simple geometry and castings with complicated geometry are both applicable in terms of casting shape. Of course, lost foam casting has numerous advantages, but it also has limitations. When compared to traditional sand casting, lost foam casting avoids the process of core building and core lowering; nonetheless, lost foam casting requires the design and manufacture of a foam forming mold, which takes time. Furthermore, the interior sprue size of lost foam casting is big, which complicates cleaning. Furthermore, the reaction of metal liquid and foam pattern lowers the temperature of the front of metal liquid, reducing the fluidity of molten metal and affecting casting quality. Because of its poor strength, the foam pattern tends to flex during the dry sand compaction process, resulting in casting shape deviation.