-
-
-
Total payment:
-
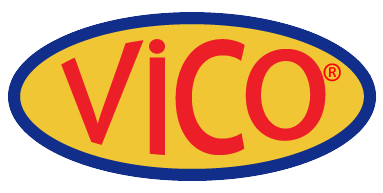
Foundry Industry: Formation and Development
Posted by Vico Casting Export Company Limited at 24/11/2021
A branch of industry that produces castings by filling molds with molten alloys. The annual volume of foundry production in the world is more than 80 million tons, of which about 25 percent is produced in the USSR (1972).
Casting is used to produce an average of about 40 percent (by weight) of stock for machine parts, but in some areas of machine building, such as machine-tool manufacture, the proportion of cast parts is 80 percent. Machine building consumes about 70 percent of all cast stock, the metallurgical industry consumes 20 percent, and 10 percent is used in sanitary engineering. Cast parts are used in metalworking lathes, internal-combustion engines, compressors, pumps, electric motors, steam and hydraulic turbines, rolling mills, agricultural machines, motor vehicles, tractors, locomotives, and railroad cars. A considerable volume of cast products, particularly from nonferrous alloys, is used in aircraft construction, the defense industry, and instrument-making. The foundry industry also produces water and sewer pipes, bathtubs, radiators, heating boilers, and furnace parts.
The use of castings is widespread because they may be produced with a shape that approaches that of the finished articles more closely than the shape of blanks produced by other methods, such as forging. Stock of varying complexity may be produced by casting without large machining allowances, which reduces the consumption of metal and the expenditures for machining and ultimately lowers the cost of the articles. Casting may be used to produce articles of virtually any weight, ranging from a few grams to hundreds of tons, with walls a fraction of a millimeter to several meters thick. The most important alloys used in the production of castings are gray, malleable, and alloy cast iron (up to 75 percent of all castings by weight), carbon and alloy steel (more than 20 percent), and nonferrous alloys (copper, aluminum, zinc, and magnesium alloys). The area of use of cast parts is constantly broadening.
History. The production of cast items was known from ancient times (second and first millennia B.C.) in China, India, Babylonia, Egypt, Greece, and Rome, where it was used for arms, religious articles, objets d’art, and domestic articles. Byzantium, Venice, Genoa, and Florence were famous for their cast products in the 13th and 14th centuries A.D. Bronze and iron cannon, cannonballs, and bells were cast in Russia (in the Urals) in the 14th and 15th centuries. A “cannon shop,” the first foundry, was built in Moscow in 1479. Foundries were built in Tula, Kashira, and other cities during the reign of Ivan IV. In 1586, A. Cho-khov cast the Tsar’s Cannon (about 40 tons).
Foundry production increased during the reign of Peter I, when foundries were built in the Urals, as well as in the south and north of the country. Iron castings were exported during the 17th century. Remarkable examples of foundry art have been created in Russia, including the Tsar’s Bell, weighing more than 200 tons (1735; I. F. and M. I. Matorin); the 22-ton Bronze Horseman monument to Peter I (1782; E. Falconet); the monument to K. Minin and D. M. Pozharskii (1816; V. P. Ekimov); and the sculpture groups on the Anichkov Bridge in St. Petersburg (1850; P. K. Klodt). One of the largest castings in the world, a 650-ton anvil of a steam hammer (the lower part, which receives the impact), was produced at the Perm’ Foundry in 1873. The skill of the foundrymen at the old Russian foundries, such as the Kasli, Putilov, Sormovo, and Kolomna foundries, is well known.
The first attempts at scientific substantiation of some casting processes were made by R. de Réaumur, M. V. Lomonosov, and other scientists, but until the 19th century, the accumulated experience of master foundrymen was used in casting. The theoretical foundations of foundry technology were laid and scientific methods used in solving specific production problems only in the early 19th century. The works of D. Bernoulli, L. Euler, and M. V. Lomonosov presented a solid basis for the development and improvement of foundry technology. The works of the Russian scientists P. P. Anosov, N. V. Kalakutskii, and A. S. Lavrov furnished the first scientifically based explanations of the processes of crystallization and the appearance of liquation and internal stresses in castings and provided means of improving the quality of castings. In 1868, D. K. Chernov discovered the critical points of metals. His studies were continued by A. A. Baikov, A. M. Bochvar, and V. E. Grum-Grzhimailo and later by N. S. Kurnakov and other Russian scientists. D. I. Mendeleev’s studies were of great importance to the foundry industry.
The rate of development of the foundry industry accelerated during the Soviet period. Aluminum casting was begun in 1922; magnesium casting, was in 1929. Modernization of existing foundries and construction of new foundries was begun in 1926. Highly mechanized foundries with annual production capacities of up to 100,000 tons were built and put into service. The reequipment and mechanization of foundries in the USSR was accompanied by the adoption of new equipment and the generation of the theoretical foundations of manufacturing processes and the design of foundry equipment. The Soviet scientific school, among whose founders were P. N. Aksenov, N. N. Rubtsov, L. I. Fan-talov, and Iu. A. Nekhendzi, began to form during the 1920s.
Technology. Foundry production is varied and is divided as follows: (1) according to the method of filling the mold—ordinary, centrifugal, and pressure-die casting; (2) according to the method of production of the mold—single-use mold casting, casting with multiple-use ceramic or sand-and-clay molds (semipermanent molds, which last for up to 150 castings, with repairs), and casting with multiple-use (permanent) metal molds, such as chill molds, which can withstand several thousand castings. Production of blanks and billets by casting uses single-use sand molds and self-hardening shell molds. Single-use molds are made by means of a pattern assembly and a mold box. The pattern assembly consists of the casting pattern itself, which is designed for producing in the mold the shape of the cavity desired in the casting, and a core box for the production of casting cores, which are designed for shaping the interior or complex exterior parts of castings. The patterns are mounted on pattern plates, on which mold boxes filled with the molding mixture are placed. The completed drag is taken off the pattern plate and rotated by 180°, and the core is installed in the mold cavity. Then the cope and drag are mated and fastened together, and the mold is filled with molten alloy. After hardening and cooling, the casting is knocked out of the mold assembly, together with the gating. The casting is then cleaned to produce the finished stock.
Production of castings in single-use sand molds is the most widespread method in the industry. It is used for the production of a variety of castings from various alloys. The castings may have any desired size and shape. The industrial process of casting in sand molds (Figure 1) consists of a series of sequential operations: preparation of materials, preparation of the mixtures for molds and cores, production of molds and cores, installation of cores and assembly of molds, melting of metal and pouring into molds, cooling of the metal and knockout of the finished casting, cleaning of the casting, heat treatment, and finishing.
Figure 1. Basic operations of the industrial process of production of castings in sand molds
The materials used for the production of single-use molds and cores are divided into the initial molding materials and molding sands; the average weight of these materials is 5–6 tons per ton of usable castings per year. Spent molding sand knocked out of the mold boxes is used in the preparation of fresh molding sand, which also contains fresh clay-sand or bentonite-type materials, additives to improve the properties of the mix, and water. The core sand mix
Usually consists of quartz sand, binders (oil, resin, and other materials), and additives. The mixtures are prepared in a fixed sequence in mixing equipment, which includes screens, driers, mills, crushers, magnetic separators, and mixers.
Molds and cores are produced on special molding equipment and machines. The mixture poured into a mold box is compacted by shaking or compression or by both methods simultaneously. Large molds are filled using sand slingers; sand-blowing machines are used less frequently. The molds in the mold boxes and the cores formed in the core boxes undergo heat drying or chemical hardening—for example, in casting in self-hardening molds. Heat drying is performed in foundry driers, and cores may also be dried in the heated core boxes. The assembly of molds consists of installation of the cores, mating of the mold halves, and fastening of the molds with clamps or weights, which are placed on the cope to prevent them from opening during pouring. A pouring basin made of core sand mix or molding sand is sometimes installed on the mold.
Metal is melted in furnaces of various types and has various output levels, depending on the composition of the alloy. Cast iron is most frequently produced in cupola furnaces, but electrically heated crucible, electric arc, induction, and channel furnaces are also used. Some ferrous alloys, such as white cast iron, are produced sequentially in two furnaces—for example, cupola and electric furnaces (the duplex process). The melt is poured into molds from ladles, which periodically receive quantities of melt from the melting furnace. The hardened castings are usually knocked out using vibrating screens or pneumatic knockouts. In the process, the molding sand drops through the screen and is conveyed to the mixture-preparation section for reprocessing, and the castings are transported to the cleaning section. The cleaning procedure involves removal of burned-on molding sand, knocking off (cutting off) the gating elements, and grinding off excess metal and the remains of the gating. These operations are performed in tumbling barrels and in shot-blasting and shot-slinging installations. Large castings are cleaned by the hydraulic method in special chambers. Cutting and grinding operations on castings are performed by pneumatic chisels and abrasive tools. Nonferrous metal castings are finished on lathes.
To attain the required mechanical properties, most steel, malleable cast-iron, and nonferrous metal castings undergo heat treatment. After the quality of the castings is checked and any casting defects are repaired, the cast articles are painted and sent to warehouses for finished goods.
Mechanization and automation. Most of the operations in the foundry industry are very labor-intensive and take place at high temperatures, with the evolution of gases and quartz-containing dust. To reduce the labor requirements and create normal sanitary and hygienic working conditions in foundries, various means of mechanization and automation of the technological processes and transportation operations are used. The introduction of mechanization into the foundry industry dates to the mid-20th century, when sand mullers, sifters, and mixers were used for preparing molding mixtures and sandblasters were used for cleaning castings. Simple molding machines were designed for manual filling of molds; hydraulic presses appeared later. Molding machines with pneumatic shaking appeared in the 1920s and were rapidly adopted. An attempt was made to substitute machines for manual labor in every operation: equipment for the production of molds and cores and devices for the knockout and cleaning of castings were improved; transportation of materials and finished castings was mechanized, and conveyors and methods for flow production were introduced. The subsequent growth of mechanization is reflected in the design of improved machines, automated casting machines, and casting production lines, and in the introduction of complete automation in various production areas and foundries.
The most labor-intensive operations in foundry production are molding, production of cores, and cleaning of the finished castings. The engineering operations in these areas are maximally mechanized and partially automated. The introduction of integrated mechanization and automation is particularly effective in the foundry industry. Automated lines for molding, assembly of molds, and pouring, as well as cooling and knockout of castings, are promising. For example, molding, pouring, and knockout are automated in the foundry line of the Swiss Bührer-Fischer system (Figure 2). Satisfactory performance has been achieved with an installation for automated pouring of molds on a continuously moving conveyor (Figure 3). The weight of the molten alloy required to fill the molds is controlled by an electronic instrument, which takes into account the capacity of a given mold. The installation is equipped with an automatic system for preparing the molding sand, monitoring its quality, and regulating its preparation (the Swiss Moldability Controller system).
Figure 2. Automatic line of the Bührer-Fischer system (Switzerland) for preparation of molds, casting, and knockout of castings
Straight-through, continuous-operation drums with shot-slinging devices are used for finishing operations (cleaning and deburring of castings). Large castings are cleaned in continuous-operation chambers, within which the castings are moved on conveyors. Automatic cleaning chambers have been designed for castings with cavities of complex shapes. The Omco-Pangborn company (USA - Japan) developed the Robot chambers. Each chamber is an independent mechanism for the transportation of castings that operates automatically, executing commands received from the guidance modules, which are arranged on a monorail transportation system. A hanger, from which the casting is automatically suspended, rotates in the cleaning zone with an optimum speed according to a preset program. The doors of the chamber are opened and closed automatically.
Figure 3. Installation for automatic pouring on a conveyor (H. Fischer plant, Switzerland)
In mass production, the preliminary (rough) smoothing of castings (stripping) is performed in foundries. During this operation, the reference surfaces of castings for subsequent processing on transfer lines in the machine shops are also prepared. The finishing operations may also be performed on transfer lines. An automatic line of the Japanese Noritake Company for cleaning the blocks of motor-vehicle engines is shown in Figure 4. Such a line makes possible the processing of 120 blocks per hour.
Figure 4. Automatic line for cleaning engine blocks, with polishing assemblies (Noritake Company, Japan)
Opportunities for mechanization and automation in the foundry industry increased significantly after the development of basically new industrial casting processes, such as production of shell molds, or the Kroning process (Federal Republic of Germany, 1940’s), fabrication of cores in cold core boxes (Great Britain, 1950’s), and fabrication of cores with hardening in hot core boxes (France, 1960’s). The use of the lost-wax method in the industry for the production of precision castings began as early as the 1940s. All operations of this process were soon mechanized. Fully automated lost-wax foundry production in the USSR is 2,500 tons of small castings per year.
REFERENCES
Nekhendzi, Iu. A. Stal’noe lit’e. Moscow, 1948.
Girshovich, N. G. Chugunnoe lit’e. Leningrad-Moscow, 1949.
Fantalov, L. I. Osnovy proektirovaniia liteinykh tsekhov. Moscow, 1953.
Rubtsov, N. N. Spetsial’nye vidy lit’ia. Moscow, 1955.
Rubtsov, N. N. Istoriia liteinogo proizvodstva v SSSR, 2nd ed., vol. 1, Moscow, 1962.
Aksenov, P. N. Tekhnologiia liteinogo proizvodstva. Moscow, 1957.
Aksenov, P. N. Oborudovanie liteinykh tsekhov. Moscow, 1968.
D. P. IVANOV and V. N. IVANOV
Source: Collector
Tags :
news