-
-
-
Total payment:
-
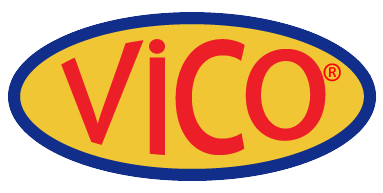
How are bearing balls made?
Posted by Vico Casting Export Company Limited at 20/02/2023
Bearing balls are a type of ball bearing component that allows for smooth, friction-free rotary motion. They are typically made of steel, but other materials such as silicon nitride ceramic, plastic, or even glass can also be used.
Steel bearing balls are by far the most common ball material, with tens of millions manufactured each year. They are nearly perfectly round and polished to a mirror-like finish to provide precision rotary motion in machines, power tools, motors, power transmission, and a wide range of other applications.
The slug
Steel wire or rod is used to make metal bearing balls. The wire or rod is cut into small pieces called slugs during the first step of the process. The slug's volume is slightly greater than that of the finished ball. Following machining steps remove the excess material. The material has not yet hardened and is somewhat malleable at this point. This is necessary in order for the slug to be formed into a spherical shape in the following manufacturing step.
Heading
The slug is then fed into a header machine, where the balls undergo a cold-forming process known as heading. Cold heading involves placing the slug between two semi-spherically shaped dies and shaping it under pressures ranging from 10 to 20 tons. It is a high-speed process that can be very loud, especially with large-diameter balls, necessitating the use of ear protection by machine operators. Heading shapes the slug into a raw ball, which is a spherical shape. There is still some excess material to be removed.
Flashing
The excess material, known as flash or burrs, must be filed away. This is accomplished during the flashing, also known as filing, process. This removes the flash, but they are still not perfectly round and the metal is soft. Manufacturers use two different machining variations, but both involve rolling the balls between metal plates.
1. To remove flash, roll them between heavy cast-iron plates that rotate in opposite directions.
2. To remove flash, the balls are passed between grooves in two metal plates, one rotating and one stationary.
Soft grinding
Some manufacturers will then go through a soft grinding process with the balls. It is called soft because the material has not yet hardened. This operation is similar to flashing, but instead of one of the metal plates, an abrasive grinding stone is used.
Heat treatment
After the excess material has been removed and the balls are relatively round, they are heat-treated to harden and strengthen them. The balls are heated to around 815°C before being quenched in an oil bath. They are heated to a much lower temperature once more. Approximately 163° C, resulting in a through-hardened ball.
Descaling
The balls are discolored and covered in oxide deposits after heat treatment. Descaling is a process used to remove these deposits from the balls. Descaling entails removing the buildup on the balls with a chemical agent, usually an acidic compound.
Grinding
The hardened and relatively round balls are nearing the end of the manufacturing process. The balls will then be ground to size and improve roundness geometry. The balls are rolled between a steel plate and a fine-grit grinding wheel, similar to the soft grinding process described earlier.
Lapping
Lapping the balls is the final step in the process. Lapping is a superfinishing process that improves the surface finish or geometry of the balls while removing small amounts of material to achieve the required tight tolerances.
The balls are rolled between two hardened steel plates, one of which is fixed and the other which rotates at a low speed. The balls are now perfectly round and mirror-like in appearance.
Finishing
After the manufacturing process is finished, they are washed to remove any remaining residue. Finally, the clean balls are inspected and sized for scratches. Even though the balls all have the same nominal outside diameter, there are minor variations. The geometric tolerances of the bearing are defined by the ball grade. The tighter the tolerances, the lower the grade number. The grade number is proportional to the sphericity and diameter variation of the balls. Tolerances are extremely tight, with very little variation between balls.