-
-
-
Total payment:
-
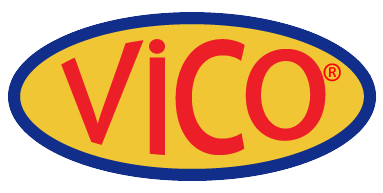
Overview of lost foam casting's solidification properties
Posted by Vico Casting Export Company Limited at 28/02/2023
Solidification is the gradual cooling of a metal liquid into a solid state during the lost foam casting molding process. The heat transfer during the solidification process exhibits the three different heat transfer modes found in nature (heat conduction, heat convection, and heat radiation). The primary characteristic of lost foam casting solidification is the requirement for heat transfer from the metal liquid to the environment through the coating layer during solidification. This slow solidification rate results in generally coarse casting grains. There are numerous causes for the lost foam casting process's slow solidification:
(1) Since the dry sand in the sand mold is devoid of water, less heat is lost during the gasification of water in the mold;
(2) On the other hand, it increases sand filling process stability, which affects sand filling process heat transfer;
(3) The refractory coating's characteristics are also different from those of the conventional cavity gravity casting. Heat in the cavity cannot diffuse outward as easily because of the refractory coating.
The microstructure and properties of castings are directly impacted by the rapid and slow solidification of lost foam casting products. Therefore, it is possible to effectively control the internal quality of products by managing the solidification process of lost foam castings. To obtain the law of cooling and solidification and accurately predict potential defects of lost foam castings, the heat transfer in the cooling and solidification process of lost foam castings is modeled and the heat transfer equation is solved.