-
-
-
Total payment:
-
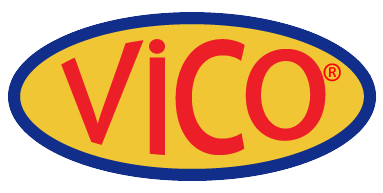
Sand casting for molding: investment casting of impellers
Posted by Vico Casting Export Company Limited at 02/03/2023
1. Molding materials
The most crucial component in the creation of casting is the molding material for an impeller investment casting. In order to determine the surface quality of the blank, it is related to the type of thermal action and chemical reaction when molten steel contacts it. High demands are placed on the fire resistance of molding sand in the casting of stainless steel because the high casting temperature makes it simple to produce casting surface flaws like sand sticking, which negatively affects the surface roughness of castings.
High thermal stability and fire resistance (> 1700 °C) are characteristics of chromite ore. Chemically speaking, it is essentially neutral. It has the advantages of having good thermal conductivity and is difficult to react with molten steel and stick to sand. As a result, in the process design, quartz sand is used as back sand, chromite CO2 hardened sodium silicate sand is used as surface sand, and a zircon powder coating is applied. The table displays the ratio (mass ratio) and characteristics of sodium silicate CO2 hardened sand, which is used as the core sand and casting surface sand for stainless steel parts.
2. Process
(1) The ratio of back sand to other processes is the same as that of surface sand, with the exception that quartz sand is used in place of chromite sand.
(2) Choosing the proper raw sand is the first step in guaranteeing the quality of the mold. Whenever possible, choose natural chromite sand with round particle shapes. The impeller investment casting sand casting size and wall thickness should be taken into consideration when choosing the raw sand particle size. The improvement of the sand mold's strength and the reduction of the impeller investment casting's surface roughness is made possible by the sand's fine particle size and dispersed sieve number. Additionally, the water content of raw sand must be controlled and the mud content of raw sand must be less than 2%. Typically, a drying procedure is needed. 100% 40/70 mesh chromite sand was used as surface sand in the experiment, with a focus on 50 mesh.
(3) Choose sodium silicate with a reasonable modulus and high quality. The sodium silicate supply is currently on the conservative side. The quality of the sodium silicate offered by various manufacturers varies greatly and cannot be exchanged. As much as possible, transparent, colorless liquids should be used. In the summer, a low modulus of 2.0 to 2.3 should be used; in the spring and the fall, a modulus of 2.4 to 2.6 can be used; and in the winter, when the ambient temperature is low, a high modulus of 2.7 to 3.2 should be chosen.