-
-
-
Total payment:
-
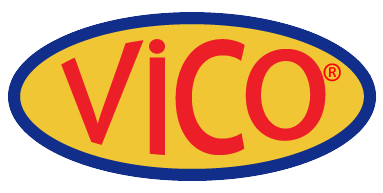
Cold shuts defect in castings
Posted by Vico Casting Export Company Limited at 12/12/2022
Cold shuts are more common on level surfaces with rather thick walls. As a result, cohesive material may separate, leaving holes, blank areas, rounded edges, and overlaps. Cold shuts (cold laps) in pressure die casting can be detected by very tiny and thin foliation cleavages.
Cold shuts result from the premature solidification of the melt during casting, which can be caused by insufficient casting or mold temperatures, casting height, or casting velocity (see Mold filling time, Mold filling time in pressure die casting). Furthermore, insufficient gas permeability may result in overpressure within the mold, slowing or decelerating metal flow. Cold closures can also be caused by incorrect metal casting characteristics.
Insufficient ingot temperatures, too slow mold filling with insufficient venting, and non-metal contaminations in the melt are the most common reasons for this fault in gravity die casting.
The most common causes of pressure die casting failure include flaws in the casting piston movement or improper selection of the changeover point from slow shot to quick mold filling phase, as well as insufficient casting flow and gating design.