-
-
-
Total payment:
-
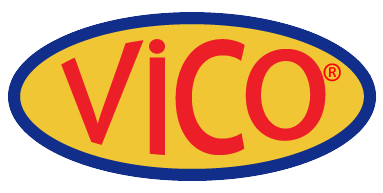
Different types of casting defects
Posted by Vico Casting Export Company Limited at 22/11/2022
Types
1. Gas Porosity: Blowholes, open holes, pinholes
2. Shrinkage defects: shrinkage cavity
3. Mold material defects: Cut and washes, swell, drops, metal penetration, rat tail
4. Pouring metal defects: Cold shut, misrun, slag inclusion
5. Metallurgical defects: Hot tears, hot spot.
1. Shift or Mismatch: The problem was created by a misalignment of the top and lower parts of the casting, as well as a misplacement of the core at the parting line.
Cause :
(1) Inadequate alignment of higher and lower parts during mold preparation.
(2) Flask misalignment (a flask is a type of tool used to contain a mold in metal casting. It can be square, round, rectangular, or any other shape that is convenient).
2. Swell : The molten metal pressure causes the mold chamber to enlarge, resulting in localized or overall casting enlargement.
Causes
(i) Defective or improper ramming of the mold.
3. Blowholes: Blowholes are generated when gases caught on the surface of a casting owing to solidifying metal form a circular or oval cavity. These flaws are always present in the mold's cope.
Causes :
(i) Excessive moisture in the sand.
(ii) Low Permeability of the sand.
(iii) Sand grains are too fine.
(iv) Too hard rammed sand.
(v) Insufficient venting is provided.
4. Drop: Drop defects occur when the upper surface of the sand cracks and sand pieces fall into the molten metal.
Causes :
(i) Soft ramming and low strength of sand.
(ii) Inadequate molten metal fluxing Fluxing refers to the addition of a substance to molten metal in order to remove impurities. Impurities from the molten metal can be easily removed after fluxing.
(iii) Insufficient reinforcement of sand projections in the cope.
5. Metal Penetration: These casting flaws manifest themselves as an uneven and rough surface of the casting. When the sand grain size is big, the molten metal fuses with the sand and hardens, resulting in a metal penetration flaw.
Causes :
(i) It is caused due to low strength, large grain size, high permeability and soft ramming of sand. Because of this the molten metal penetrates in the molding sand and we get rough or uneven casting surface.
6. Pinholes:
They are very minute holes, around 2 mm in diameter, that develop on the surface of the casting. This flaw occurs as a result of hydrogen gas dissolving in molten metal. When the molten metal is poured into the mold cavity and begins to solidify, the solubility of the hydrogen gas reduces and it begins to escape, leaving behind a tiny number of pinholes.
Causes :
(i) Use of high moisture content sand.
(ii) Absorption of hydrogen or carbon monoxide gas by molten metal.
(iii) Pouring of steel from wet ladles or not sufficiently gasified.
7. Shrinkage
Shrinkage is the formation of a cavity in casting as a result of volumetric contraction.
Causes :
(i) Uneven or uncontrolled solidification of molten metal.
(ii) Pouring temperature is too high.
8. Cold Shut
It is a sort of surface imperfection with a visible line on the surface. When liquid metal enters the mold through two gates, and these two streams of molten metal meet at a junction with low temperatures, they do not fuse and solidify, resulting in a cold shut (appear as line on the casting). It appears to be a crack with a rounded edge.
Causes:
(i) Poor gating system
(ii) Low melting temperature
(iii) Lack of fluidity
9. Misrun: Misrun occurs when molten metal solidifies before completely filling the mold cavity, leaving a space in the mold.
Causes:
(i) Low fluidity of the molten metal.
(ii) Low temperature of the molten metal which decreases its fluidity.
(iii) Too thin section and improper gating system.
10. Slag Inclusion: This flaw occurs when molten metal containing slag particles is poured into the mold cavity and solidifies.
Causes :
(i) The presence of slag in the molten metal