-
-
-
Total payment:
-
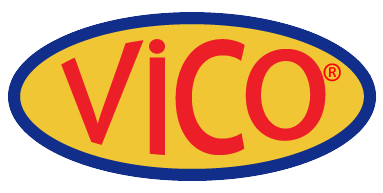
Extrusion
Posted by Vico Casting Export Company Limited at 15/11/2022
Extrusion is a method of producing long, straight metal parts. Cross-sections can be produced in a variety of shapes, including solid round, rectangular, L shapes, and T shapes. Tubes, among many other things. Extrusion is accomplished by using a mechanical or hydraulic press to squeeze metal in a closed cavity through a tool known as a die.
Schematic of metal extrusion process
In the stock, extrusion generates compressive and shear forces. Because no tensile is produced, high deformation is possible without tearing the metal. The cavity containing the raw material is lined with a wear-resistant material. This can withstand the high radial loads produced when the material is pushed through the die.
Extrusion is a method of producing objects with a fixed cross-sectional profile. The desired cross-section of a material is pushed or drawn through a die. The ability to create very complex cross-sections and work materials that are brittle due to only compressive and shear stresses are the two main advantages of this process over other manufacturing processes. It also produces
Extrusions, while frequently reducing the need for secondary machining, do not have the same dimensional accuracy or surface finish as machined parts. Steel has a surface finish of 3 µm, while aluminum and magnesium have a finish of 0.8 µm. However, this process can generate a wide range of cross-sections that would be difficult to produce cost-effectively using other methods. Steel has a minimum thickness of about 3 mm, whereas aluminum and magnesium have a minimum thickness of about 1mm. Steel has a minimum cross section of 250 mm2, while aluminum and magnesium have smaller cross sections. Aluminum and magnesium have minimum corner and fillet radii of 0.4 mm, while steel has a minimum corner radius of 0.8 mm and a fillet radius of 4 mm.
Cold Extrusion :
Cold extrusion is a process that takes place at room temperature or slightly higher temperatures. This process can be used for most materials, provided that the tooling is robust enough to withstand the stresses created by extrusion. Lead, tin, aluminum alloys, copper, titanium, molybdenum, vanadium, and steel are examples of metals that can be extruded. Cold extruded parts include collapsible tubes, aluminum cans, cylinders, and gear blanks.
The advantages of cold extrusion are:
- No oxidation takes place.
- Good mechanical properties due to severe cold working as long as the temperatures created are below the re-crystallization temperature.
- Good surface finish with the use of proper lubricants.
Hot Extrusion :
Hot extrusion occurs at relatively high temperatures, ranging from 50 to 75% of the metal's melting point. Pressures can range from 35 to 700 MPa. Good lubrication is required due to the high temperatures and pressures and their detrimental effect on die life and other components.
At lower temperatures, oil and graphite are used, whereas at higher temperatures, glass powder is used. Extrusions are commonly used to manufacture trim parts for automotive and construction applications, window frame members, railings, and aircraft structural parts.