-
-
-
Total payment:
-
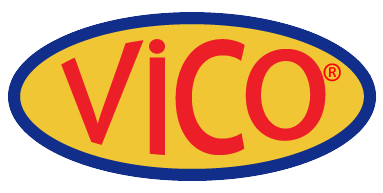
Grinding Balls Manufacturing Process
Posted by Vico Casting Export Company Limited at 05/08/2022
The grinding ball is a grinding medium used in ball mill and material used in grinding mills, widely used in metallurgical mines, cement building materials, thermal power generation, flue gas desulfurization, magnetic materials, chemical industry, coal water slurry, pellet, slag, ultrafine powder, fly ash, calcium carbonate, quartz sand, and other industries ball mill. But how to produce the qualified grinding balls? What’s the grinding balls manufacturing process?
Manufacturing grinding balls, there are four essential steps. First melting, second molding, third separating, and the last heat treatment.
1. Melting. The furnace the factories most used are the medium frequency induction furnace, fast and stable. It’s easy to add the ferrochrome and the other elements inside. The raw material we required is the iron scrap. Grey iron is not good enough for producing grinding balls. Because of the carbon contents too much. After melting, we have to clean up the slags and pour the pure liquid iron into the metal mold. To ensure the right chemical composition, after melting and before pouring, the operator should get some to do the analysis test. Its each chemical composition is right. Then we can do the next step.
2. Molding. There is different method to form the balls. For instance, we can use the manual metal mold to produce or sand mold; or we can use the automatic machines to produce, like automatic sand-lined metal mold grinding balls production line; or Disa production line, or any other green sand molding line. With the help of the pouring machine or pouring ladle, pouring the liquid into the prepared mold. For manufacturing grinding balls, we required one-time pouring. If the last pour is unfilled, then the formed balls we regard as the discarded product.
3. Separating. As we all know, if we want to ensure the no holes inside the balls and get better quality of the inner structure, there will be a pouring gate that is used for feeding enough molten iron to the balls. So after the balls are formed, they are connected with the runners and gates. Have to separate. There are also two methods, one is an auto separating machine that can process grinding balls over 40mm, and the hourly productivity can be up to 3-5tons. This type is suitable for medium and large grinding balls factories to achieve high efficiency. Another manual method is using a separate machine; the principle is that the friction between the balls to make the separation. But for some big size balls, like dia130mm, the operator usually uses a grinder to cut. So after separating, then go to the last step.
4. Heat treatment. Heat treatment is a vital process for a good ball. This process will change the ball’s characteristics, increase the hardness, and reduce the inner stress. To achieve the formed grinding balls have good impact value and low wear rate. This process includes quenching and tempering. And the heat treatment machine also has several types with different daily processing ability.
After the above 4 steps, the excellent balls are produced and can package and sell.