-
-
-
Total payment:
-
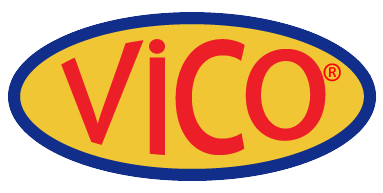
Shrinkage in sand casting
Posted by Vico Casting Export Company Limited at 08/12/2022
As they harden, most metals, including aluminum, copper, zinc, and magnesium, shrink. The degree of shrinkage is determined by the material's freezing range. Aluminium, for example, shrinks by more than 6% during solidification, but copper shrinks by less than 5%.
Solidification happens in sand casting as the molten metal is poured into the mould cavity. To limit shrinkage and eliminate faults, it is critical that this stage of the sand casting process is carried out in a highly regulated way.
Solidification shrinkage
Because metals are less dense as liquids than as solids, solidification shrinkage occurs. Risers and chills are employed to combat this issue.
Risers keep molten metal flowing into the casting as it solidifies. They are critical in facilitating directional solidification, which occurs when the metal solidifies at the farthest point first before migrating towards the riser. Using this method, the cavity forms in the riser rather than the casting.
Chills, or metal inserts, are also utilized to help risers. They aid in the equalization of the rate of solidification in the thicker sections of the metal casting.
Pattern maker’s shrinkage
When the casting is cooled to room temperature after solidification, pattern maker's shrinkage occurs. Thermal contraction causes this effect. As a result, a shrinkage tolerance must be built into the design from the start.
To account for this form of shrinkage, the pattern is made larger than the target casting size. The shrinkage allowance varies depending on the metal, but the pattern may need to be 2.5% larger than the original part. Additionally, different portions of the casting may necessitate different allowances. To produce a high-quality finished product, judging these tolerances requires talent and experience.